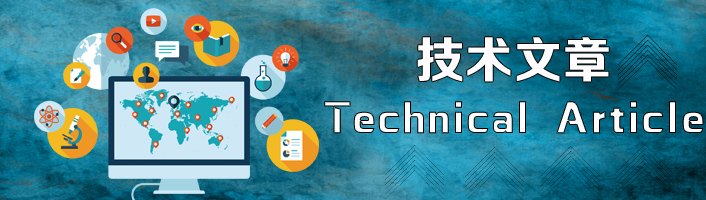
促進煙氣排放達標的重要措施——降低煙氣含氧量技術
《磚瓦工業大氣污染物排放標準》(GB29620-2013)要達在基準空氣過量系數1.7達到表1的指標。
目前的實際情況是大多數企業環評、環保驗收都能通過正常生產都不能穩定達標原因很多但主要原因有三方面:一是GB29620-2013排放標準沒有考慮磚瓦生產工藝的特點空氣過剩系數不符合行業生產工藝實際;二是磚瓦生產工藝的煙氣處理技術僅參考鍋爐、火電等其他行業的煙氣治理技術缺乏與磚瓦工藝結合的治理技術;三是缺乏燒結磚行業煙氣治理的基礎研究和科學實驗僅僅靠一些企業在摸索、試驗對行業造成重大損失。
降低煙氣含氧量是促進煙氣排放達標的重要措施下面我們重點介紹降低煙氣含氧量的幾個主要技術。
隧道窯煙熱分離處理和利用降低煙氣含氧量
即將隧道窯混合氣體中的預熱段混合煙氣、冷卻段余熱空氣分離處理和利用。
預熱段混合煙氣重點脫硫、除塵處理冷卻段余熱空氣干燥磚坯后重點除塵“煙熱分離”后降低了煙氣的含氧量解決隧道窯煙氣排放因空氣過剩系數高無法達標的問題另一方面可使脫硫設施投資和煙氣處理成本的降低。
降低入窯殘余含水率可大量減少預熱段混合煙氣的量降低煙氣含氧量
入窯殘余含水率由6%降低到2%預熱段需要帶走水分的煙氣量相對減少了一半。
提高排潮溫度減少干燥風量
降低煙氣含氧量根據計算(濕坯2.9kg、熱值300kcal/kg濕坯(折每塊磚870kcal燒失量近似按8% 、濕坯含水率按15%)。
排潮溫度60℃排潮最大能力為0.114kg/m3每kg磚坯需要大于1.22m3的熱氣。
排潮溫度45℃排潮最大能力為0.049kg/m3每kg磚坯需要大于3m3的熱氣。
排潮溫度40℃排潮最大能力為0.035kg/m3每kg磚坯需要大于4m3的熱氣;排潮溫度30℃每kg磚坯需要10m3熱氣才能帶走水蒸氣;排潮溫度25℃每kg磚坯需要20m3熱氣才能帶走水蒸氣。
降低濕坯水分減少干燥風量降低煙氣含氧量
采取靜停、窯外預干燥等技術措施減少濕坯進入干燥窯的水分能提高磚坯干燥質量和產量降低煙氣中空氣過量系數。
以每小時1萬塊坯體(濕坯按3.3kg計算)的產量為例含水率由15%降低到12%相比每萬塊少帶入990kg/h 水可減少干燥氣體量約1404+990×22=23184m3/h。
煙氣再循環(煙氣復燒)、降低煙氣含氧量
將部分低溫煙氣直接送入爐內或與空氣(一次風或二次風)混合送入爐內。因二次燃燒了煙氣中的氧氣、稀釋了氧濃度使含氧量、NOx減少。
利用煙氣所具有的低氧以及溫度較低的特點將部分煙氣再循環噴入爐膛合適位置降低局部溫度及形成局部還原性氣氛一方面降低煙氣含氧量、同時抑制NOx的生成,有利于達標排放
降低煙氣含氧量是促進煙氣排放達標的重要技術措施主要有:隧道窯煙熱分離處理和利用;降低入窯殘余含水率、可大量減少預熱段混合煙氣的量;提高排潮溫度減少干燥風量;降低濕坯水分減少干燥風量;煙氣再循環(煙氣復燒);通過選擇原料、燃料減少產生SO2、NOx、氟化物等的物質進入燒結磚工藝中。
在工藝上采取降低氧含量促進達標的措施
- “內燃燒磚法”應采用高內燃或全內燃,少投煤或不投煤。
- 應將干燥窯和焙燒窯的進車端門由單層改為雙層。
- 焙燒窯應采用較小的邊隙和頂隙。
- 無論是干燥窯還是焙燒窯,粗糙度儀均應采用窯車上下壓力平衡技術以免負壓段的車下吸入空氣。
- 應重視窯體的保溫、防漏并制定先進、合理的熱工制度。
- 不把外界粉塵帶入窯內。
燒結磚行業面臨嚴峻的環保形勢行業必須重視煙氣治理降低煙氣含氧量能促進排放達標比提高除塵脫硫的凈化效率更有效。建議燒結磚行業煙氣治理的技術路線按重要程度的權重依次分四步走:第一步首先要改造燒成、干燥工藝降低煙氣含氧量;第二步是通過選擇原料、燃料減少產生SO2、NOx、氟化物等的物質進入燒結工藝中;第三步通過各種技術手段改變燃燒條件抑制SO2、NOx生成;第四步才是對煙氣采取脫硫、除塵等治理措施即末端治理實現達標排放。
相關推薦: